Case Study Challenge
Objective
The car manufacturer faced challenges in reducing time-to-market, optimizing production efficiency, and enhancing product quality. Additionally, they sought to streamline maintenance operations and improve customer experience through proactive servicing and personalized recommendations.
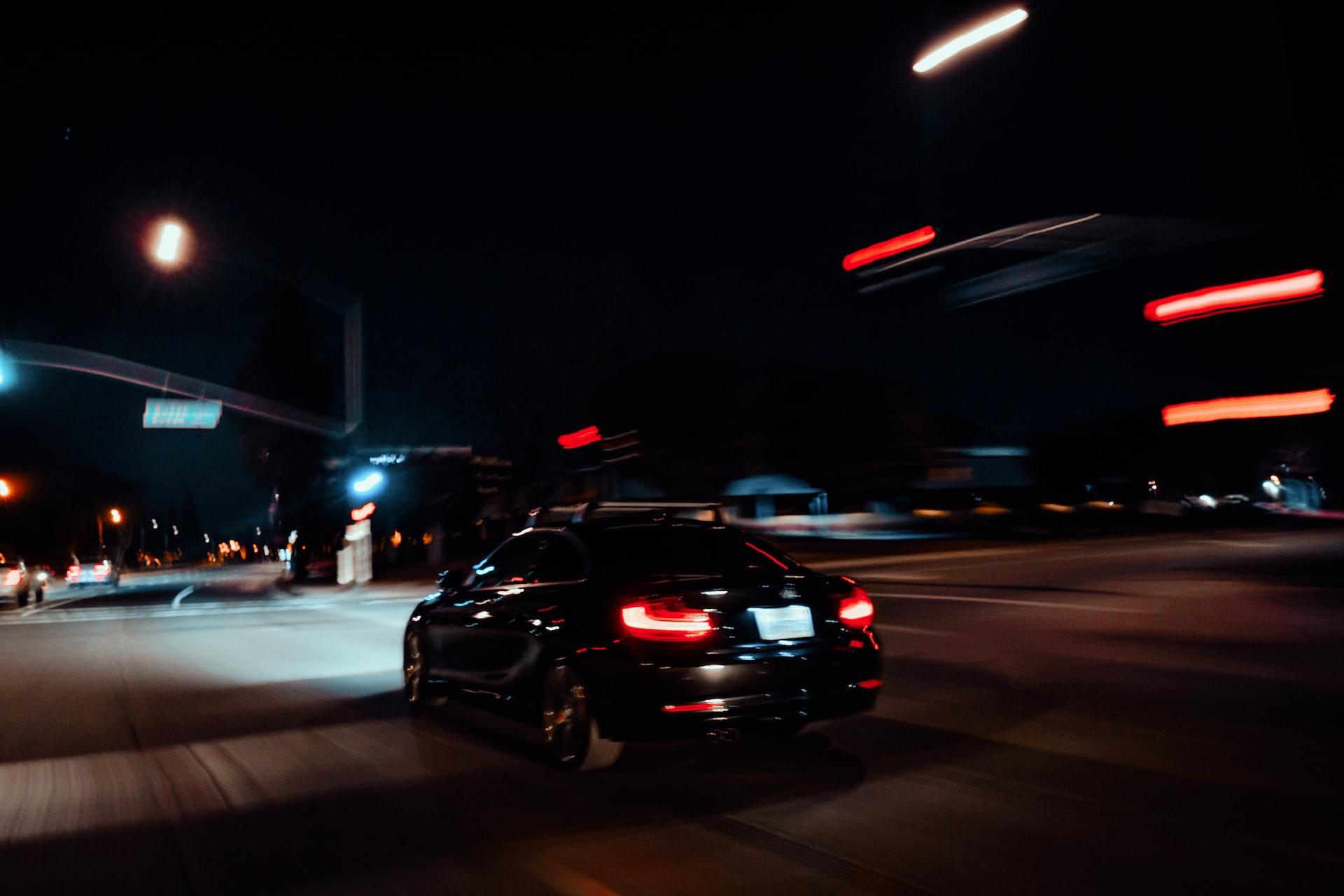
01
Solution
Objective
The implementation of a digital twin technology offered a holistic solution to address these challenges. A digital twin is a virtual replica of a physical product or process, enabling real-time monitoring, analysis, and simulation. The car manufacturer leveraged the power of digital twin technology across various stages of their operations.
02
Design and Engineering
Objective
By creating a digital twin of their vehicles, the manufacturer simulated and analyzed design variations, allowing rapid prototyping and virtual testing. This accelerated the design process, minimized physical prototypes, and enhanced overall product quality.
03
Production Optimization
Objective
Digital twins were deployed in manufacturing facilities to monitor and optimize production lines. Real-time data from sensors embedded in machines and vehicles provided insights into performance, efficiency, and quality metrics. This enabled proactive maintenance, reduced downtime, and optimized production schedules.
04
Predictive Maintenance
Objective
The car manufacturer used digital twin models to predict maintenance requirements based on real-time data collected from vehicles. This enabled proactive servicing, reduced unplanned breakdowns, and improved customer satisfaction. Predictive analytics and machine learning algorithms were applied to identify patterns and anticipate potential issues.
05
Customer Experience
Objective
The digital twin technology facilitated personalized customer experiences. Real-time data collected from vehicles allowed the manufacturer to offer customized recommendations for vehicle maintenance, upgrades, and performance enhancements. This improved customer satisfaction and fostered brand loyalty.
Results
The adoption of digital twin technology yielded significant benefits for the car manufacturer:
● Reduced time-to-market through accelerated design iterations and virtual testing.
● Enhanced production efficiency and quality through real-time monitoring and optimization.
● Proactive maintenance and reduced downtime, resulting in cost savings and improved customer satisfaction.
● Personalized customer experiences, leading to increased brand loyalty and repeat business.
Conclusion
The successful implementation of a digital twin solution enabled the car manufacturer to achieve operational excellence, drive innovation, and maintain a competitive edge in the market. By leveraging the power of digital twin technology, they streamlined their design, production, and maintenance processes, delivering higher-quality vehicles while enhancing customer experiences. This case study exemplifies the transformative impact of digital twin technology in the automotive industry and serves as a testament to its potential in driving efficiency and innovation.